tungsten carbide nozzle welding process
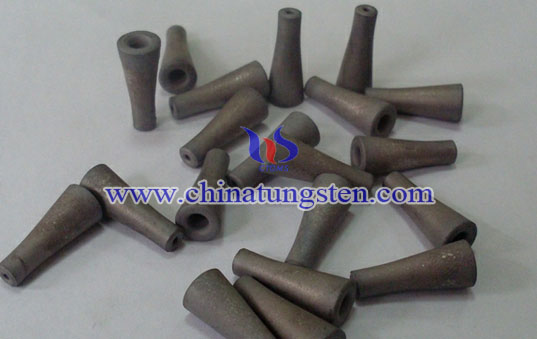
In order to improve drilling efficiency, people invented a kind of nozzle, which is longer and closer to the button. The jet-flow impacts the bottom and disperses, its the fluid up and down do not interfered, which can effectively enhance drilling rate of 28%. However, the nozzle inside structure is too complicate to manufacture by normal compression molding. So some researchers used heat pressing impregnate-powder casting to attempt. But the materials contain Cu and other soft metals, which decreases the hardness, anti-corrosion of nozzle and shortens the lifespan. Therefore, a new method brazing after compression section molding appeared. It still remains some problems that the strength of soldering seam is not good, which replaced by vacuum welding procedure.
The influence of welding temperature for quality: Welding temperature plays a significant role in welding plastic deformation, enlarging the contact area between two welding surfaces, accelerating spreading process and improving the strength and compactness of soldering seam. In addition, with the welding temperature increasing, the strength of soldering seam will improve gradually. When the temperature is running up to a certain value, the yield strength of material will remarkably reduce, the contact areas will rapidly increase and welding rate will improve a lot.
The influence of welding time for quality: In a short time, the welded surface fully physical contact gradually, and diffusion of atoms become sufficient, welding shear strength and welding rate increases by welding time steadily. However, when the strength of soldering seam reaches the strength of tungsten carbide, if adding welding time continuously, it will make tungsten carbide particles become bigger and bigger so that some micro-bore will appear and the strength of soldering seam will decrease, which because of the different spreading speed between Co and Ni. Therefore, reasonable welding time is a guarantee for improving the soldering seam strength.