Types of Tungsten Carbide Nozzle
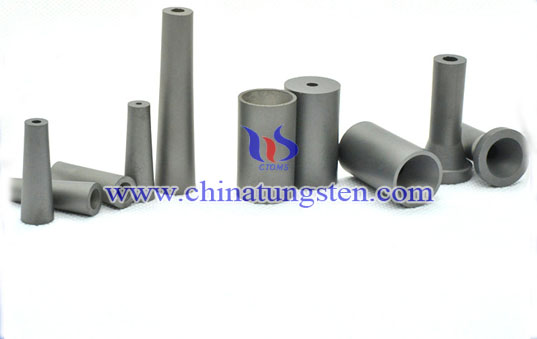
A nozzle's bore shape determines its blast pattern. Nozzles generally have either a straight bore or a restricted, venturi bore.
Tungsten carbide nozzle types:
1. Straight bore (tungsten carbide nozzle 1)
Straight Bore nozzles create a tight blast pattern for spot blasting or blast cabinet work. These are best for smaller jobs such as parts cleaning, weld seam shaping, cleaning handrails, steps, grillwork, or carving stone and other materials.
2. Conventional design long venturi (tungsten carbide nozzle 2)
3. Laminar flow design long venturi (tungsten carbide nozzle 3)
Venturi bore nozzles create a wide blast pattern and increase abrasive velocity as much as 100% for a given pressure. Venturi nozzles are the best choice for greater productivity when blasting larger surfaces. Long venturi style nozzles yield about a 40% increase in productivity compared to straight bore nozzles, while abrasive consumption can be cut approximately 40%.
4. Double venturi (tungsten carbide nozzle 4)
Double venturi and wide throat nozzles are enhanced versions of the long venturi style nozzle.
The double venturi style can be thought of as two nozzles in series with a gap and holes in between to allow the insertion of atmospheric air into the downstream segment of the nozzle. The exit end is also wider than a conventional nozzle. Both modifications are made to increase the size of the blast pattern and minimize the loss of abrasive velocity.
5. Wide throat nozzles (tungsten carbide nozzle 5)
Wide throat nozzles feature a large entry throat and a large, diverging exit bore. When matched with the same sized hose they can provide a 15% increase in productivity over nozzles with a smaller throat. When wide throat nozzles also feature a larger diverging exit bore, they can be used at higher pressures to yield up to a 60% larger pattern with lower abrasive use.
It's also a good idea to have angle nozzles available for tight spots like bridge lattice, behind flanges, or inside pipes. Many operators waste abrasive and time waiting for ricochet to get the job done. The little time it takes to switch to an angle nozzle is always quickly recovered and total time on the job is reduced.